ABOUT US
It all started in 1971, an electrician by the name of Art Van Otterloo started a small business right here in Hull Iowa. Being an electrician in the #1 cattle producing county in Iowa meant that he spent a lot of time installing and servicing cattle fountains. He eventually became a dealer for multiple fountain brands and installed hundreds of different models. Down the road his three boys would become part of the family business, thus they also frequently worked with fountains.
Over time they noticed frequent and repeat issues with the different brands. With the massive production of ethanol based products in today’s agriculture industry, we now have alot of by-products we use to feed our cattle. The biggest issue with these by-products is they make our cattle feed acidic. This means after the cattle eat they go to take a drink and drop feed out of their mouth or nose area into the water. This feed settles on the bottom of the tank and wreaks havoc on concrete and plastic tanks. The sealant the concrete fountains use is no match for the acidic water and is deteriorated in weeks. This acidic feed also settles around the heating element and bakes onto the element making it extremely inefficient and drastically shortens the life of the element. Over time they noticed frequent and repeat issues with the different brands. With the massive production of ethanol based products in today’s agriculture industry, we now have a lot of by-products we use to feed our cattle.
Same goes for the plastic water tanks, this acidic water makes the plastic extremely brittle and when livestock step in the tank they bust straight through the trough. They also use a submersible heater which gets surrounded by settled feed and runs constantly to keep the water thaw, this wastes electricity and shortens the life of the element. A few years ago they started producing plastic tanks with stainless troughs, there are two major issues with this design.
For starters, they use 22 or 24 gauge stainless steel which is thin enough to easily bend with your hands. Secondly they have heating elements that are under the trough, the issue is that when feed settles on the floor of the fountain the heat has to make it through that feed to get into the water. This means your heating elements are going to run longer than necessary. Since they use 22 or 24 gauge steel for the trough, eventually the elements are going to burn through that thin steel from running days on end to try and keep the water thawed.
We use 12 and 14 gauge 304 Stainless for the tank this is over 2mm in thickness, whereas the competitors trough is not even 1mm thick. Our heating elements are a slide in design under the trough.
This makes them extremely easy to access and keeps them out of the water, lowering the chances for stray voltage and making their life span much higher than any other company.
We also use a high flow float valve which is either on or off, it does not trickle like a regular float valve. Thus when the cattle drink and drop feed debris into the water, the next time the fountain fill it is spraying the floor clean, putting any feed debris in the water back into suspension, this keeps our fountain extremely clean and energy efficient because the heat can easily transfer into the tank instead of trying to heat through the feed like our stainless competitor.
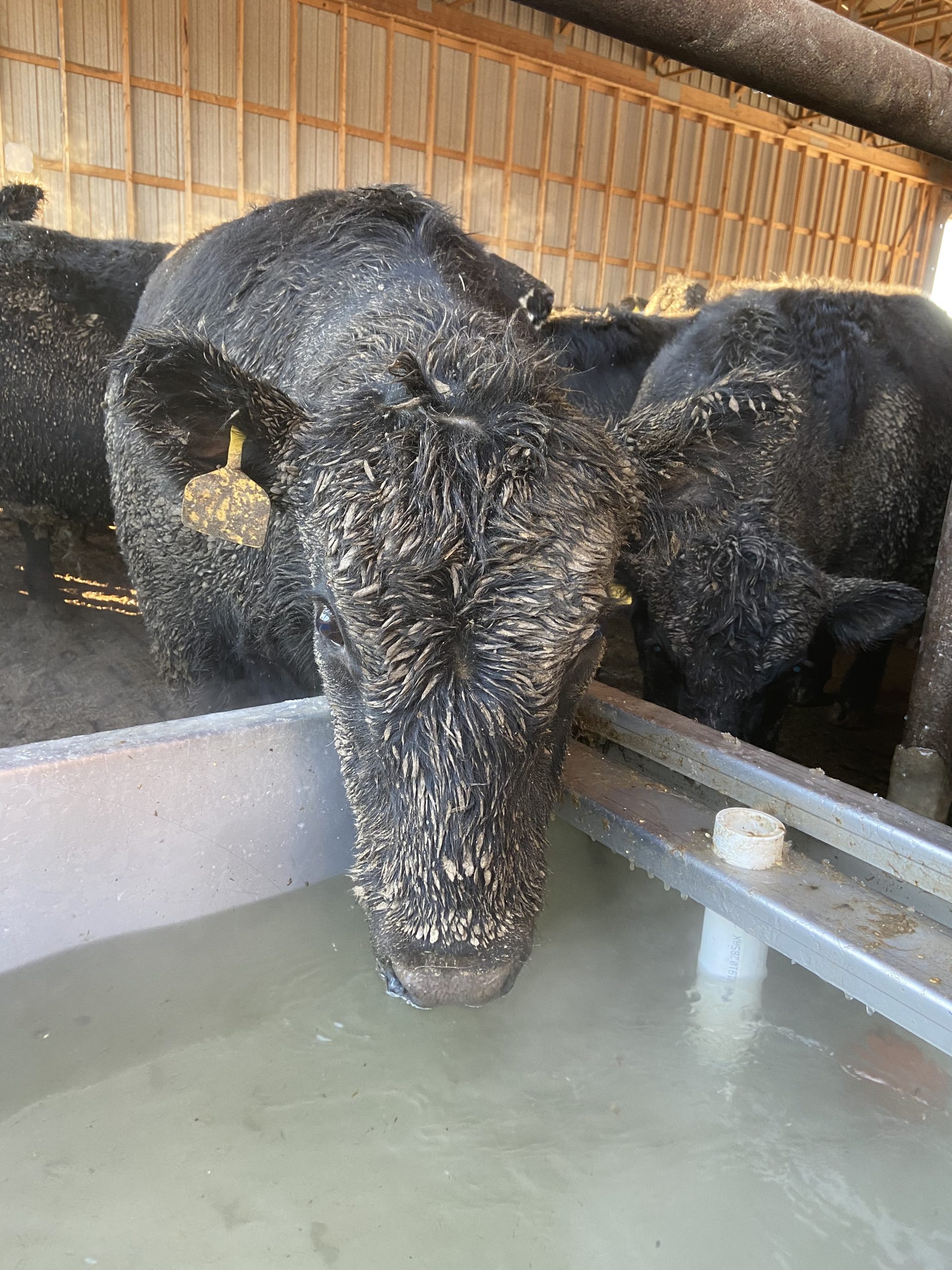